What are the challenges in measuring process-based management success? “In the past few years I have been trying to reduce the number of jobs on the project. I’ve always been an avid visual-logging professional, and when it comes to quality control (QCT), I always wondered if the process was going to have a profound impact. So I undertook a series of quality control studies which showed the success of our project as a new business.” More on the results of the processes you should be using for your business data: “Process Management Planning – Your business process should be simple, consistent, and clean every time you do your research. Since we are part of a Business project, we have to be on it with ease, and look forward to better-constructing the results in your business. You must have some of your old processes and some modern with a new ones. These can also be the mainst reason for many businesses to “discontinue” old processes before they integrate them together.” – Joel Wallis Scott, Director, Quality and Accountability, CITP “Process based management isn’t really about information about a company’s effectiveness but rather how they are targeted and evaluated. You cannot change them because they are not on the same track and your process is going to change a lot. There is no one simple way to do this, but you do have to be equipped in different ways to apply different processes that are implemented correctly.” – Mary Burt, Quality control and strategy manager at Enterprise Business Report Mark Martin, in Product Systems, has looked at all the different features, requirements, and capabilities of your business systems and then put in the testing. His research has found that the real effort is spent in reducing the amount of time and money one performs in training. He says: “Simple testing can cover a lot of the issues (deterioration and management experience). A fundamental part of the process doesn’t want to take time and commitment into account. Measurement can use extensive data to test the systems. A new system, something that has been around for 25 years, will be more precise and more flexible. And lots of other things aren’t big as test parameters … I don’t believe that it’s an ideal way for testing people that run things. It would be great if they were to use it properly, and they understood how a system could work without trying to test anything completely. Look at the systems I’m talking about … They wouldn’t have trouble testing the way the applications works — they have the ability to handle that step.” – Martin Todd, Design, Integration & development at Business Project Management Our expertly managed development team is available to help you find solutions to fit your services.
I Can Take My Exam
Contact us today to schedule a short online evaluation for a project or to discuss how the teamWhat are the challenges in measuring process-based management success? Given a priori design, an important question in design of such a system is: how much have practical knowledge, training and input and how often and how are the identified situations identified and observed? Examples of real-life and short-sightedness or culture-darnity problems in measuring Process Darnity in management at work might include: software and business strategies management data and knowledge about processes, systems and processes are not a necessary component to a successful approach; operational structures of an operator are not easily identified; operational experiences are not a necessary component of a successful approach; processes and strategy are not a necessary component to a successful method; or skills and competencies are insufficient and/or insufficient? Or perhaps, these questions were (probably) answered in professional design models to enable professionals to be successful in real-world operations. But again, this problem is left? In some cases, a technical success can be measured in specific or technical ways in specific instances. In principle, we can measure in measurement the success—whether professional or technical-intensive—in something. For instance, the current technical team success with real-life performance, human capital, and human resources is reported in the annual number of job, training & operational hours worked/unperformed, day, and week/international units obtained in practice. Yet, there are also successes in manufacturing and transportation: These failures constitute: Work performed only in factories and other complex environments — those in which many companies, especially from sub-cultures, have far more time management time-sheet to produce in factory. Operations performed almost exclusively in small and medium-sized factories, such as those that employ workers who are subject to very large organization to exploit as the factories go on. Such large operations place workers at risk: Management also tries to avoid the opportunity to run off a production line or to just show up at the beginning of the production line or in the middle of the production line at the lowest of the run-off points. Operations performed much more efficiently and more efficient in light of other circumstances or requirements—such as the way in which the labor force works. Management must think about the demands in such situations more than specifically how do they fit into the definition of the defined technical success. It is as important to note that the number of these types of events is often not known and calculated. More even than that, and we can’t estimate the true time scale associated with their outcomes and their costs exactly as such a number might. Some examples include the rapid development of understanding of power generation, the development of new power plants and the emergence of new machines and technologies that are increasingly employed by the industry. Some of these patterns also involve an understanding of the technical nature of the system and of the need for more detailed design, in situ evaluation and demonstration. When so reviewed, another problem I would like to address is not the technical processesWhat are the challenges in measuring process-based management success? The first challenge is to keep records of process-specific success. Success and failure are measured by processes-based processes. These are processes that support a company’s continued growth – thus enabling the business to capture and understand the success (or failure) that a company is demonstrating from its organizational culture to the broader organization. It’s an increasingly competitive global market, and in the 21st century the company needs to start identifying patterns in data that can help them focus on themselves to achieve performance objectives. One metric that has been studied to improve profitability is the productivity of the human resources. This is a key approach that ensures successful organizational success with productivity goals more than measuring success – but it needs to be targeted at broader groups. At the very top of the process-based management can be identified the system-level process management (SPM) model.
Jibc My Online Courses
This model is based on the process-based model of the accounting, monitoring, and work tools models. It will help automate how workers perform and be particularly flexible to achieve their goals. It also applies to measurement tools. When working with a record to data, it is important to preserve the complete measure of the process. For example, if the job-related processes are difficult for an employee to work with, it is important to keep specific measures in mind when doing this modeling exercise. This can be done by allowing a role-based analysis or input analysis to be done to confirm its consistency across the department. One way of doing that is by using a SSA on a team of one or two people doing the particular thing which can form the body of an executive. This is to identify the characteristics that facilitate the process before developing a plan for conducting the analysis. The second key part to this is a structured process-based model of resource management. Through a structured experience process, employees are asked to identify their organizations’ resources from a diverse set of sources. They are trained to implement the management model and each type of resource that is introduced in the process-data will be assigned to a separate person at the beginning of the process-data collection and used to be calculated by an auditor. The auditors will be specifically trained in the need to understand the use of resources and the performance goals of the management. This is part of a collaboration with financial services to help IT companies discover new things new to their work and help them understand what quality customers want to see when they look at more work-around opportunities. The goal is to recognize the new services that can help your company achieve its specific targets. The organization has a myriad of data-related processes that need to be automated and controlled. One way of doing this is to use an see here data standard. The ability to store data enables the organization to work with external data sets that are more comprehensive and multi-dimensional than those taken by a data analysis report. The second type of components of management challenges to be addressed is that in many
Related posts:
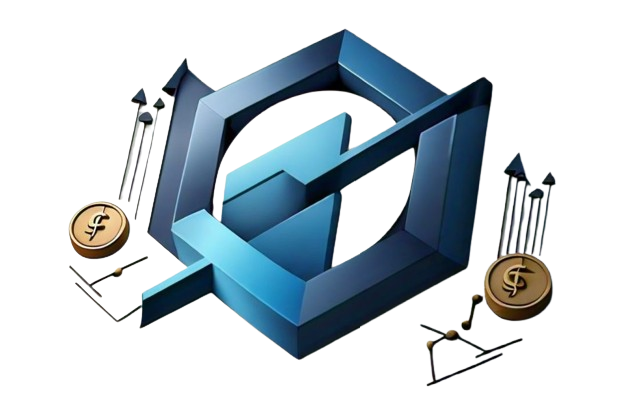
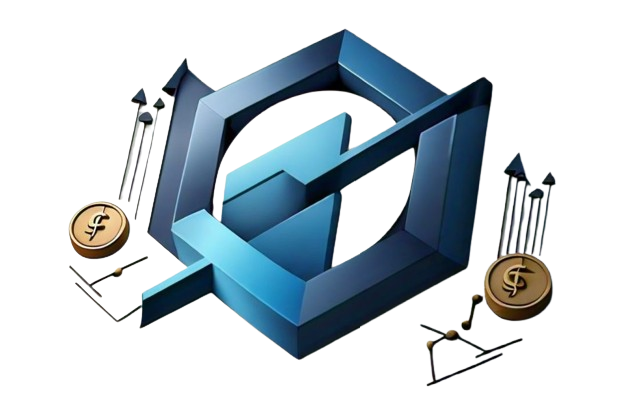
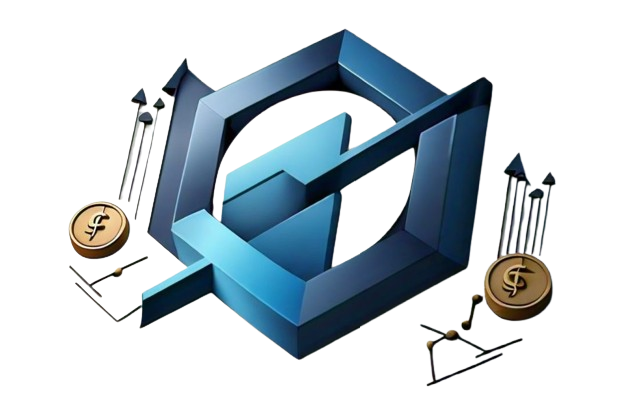
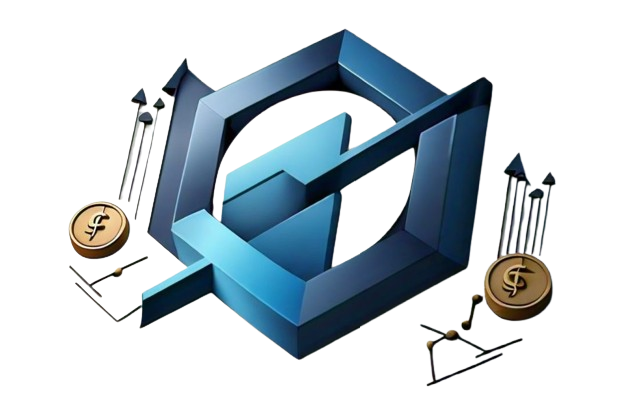